CO2回收装置
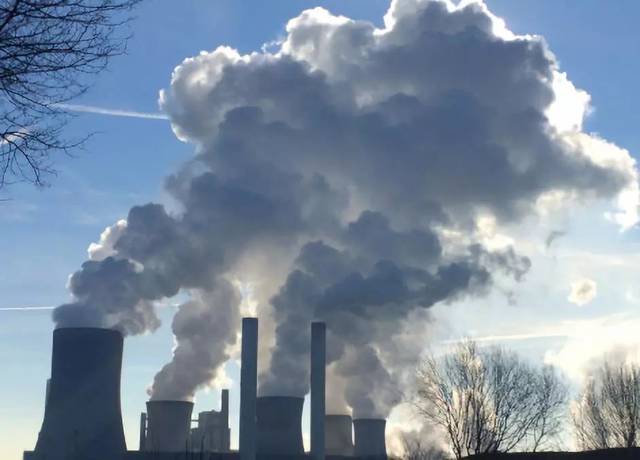
CO2回收装置是应时代发展需要的环保产品
目前,排放CO2较少的核能、水力发电以及太阳能、风能、潮汐地热能等可再生能源依旧处在初期发展阶段,到2030年全球一次能源消耗还会以石油、煤、天然气等化石能源为主,这样必然导致CO2排放量的增加。随着各个**减排压力和能源压力的增大,需要发展较清洁能源。但若要使得清洁能源取得较大进展,更多要靠技术或者经济因素来推进,比如,设法使清洁能源相比于化石能源而言更高效、更经济、更低成本。因此,现阶段需要一些措施落实,以使大气中的CO2稳定在不会引起气候变化威胁人类生存的水平,比如减少CO2的排放、CO2的储存和CO2的利用。
应时代发展的需要,开封赛普空分集团有限公司自2016年至今,陆续制造了近20套CO2回收装置,装置规模从*小每年3万吨到每年30万吨,CO2液体产品质量可以由客户选择工业级(GB/T 6052-2011 工业液体二氧化碳)和食品级(GB 10621-2006 食品添加剂-液体二氧化碳),或同时获得这两种级别的产品。这是一项兼有社会效益和经济效益的环保产品
质量为先 创新为本
CO2原料气源分类
CO2的捕集和提纯技术与CO2来源有关,可分为三个大类:
1、石灰窑气、锅炉烟道气等低CO2浓度原料气
原料气来源:石灰窑、锅炉烟囱排放气体。
主要特点:CO2浓度30%左右,有机杂质少,通常采用溶液吸收法或变压吸附法对原料气预处理提浓,将原料气CO2的浓度提高到98%。而溶液吸收法和变压吸附法各有优劣。溶液法所得的原料气中CO2纯度高,但会含对人体有毒有害的有机杂质,这来自溶液本身自带的特性。变压吸附法虽然避免了对人体有毒有害的有机杂质,但受其工艺的影响,所得的原料气中CO2纯度较低,而CO2纯度低意味着较高的液化能耗。
2、合成氨脱碳解吸气用作CO2原料气
原料气来源:在合成氨的生产过程中,净化工段脱碳解吸气送往尿素车间,一部分用于生产尿素,还剩一部分富余气体直接排放到了大气。若利用原有的水、电、汽等公用工程,对该部分CO2进行提纯液化回收,既能解决环境问题,有能产生一定的经济效益。
主要特点:CO2浓度90%左右,含有少量的CH4、N2、O2、CO、H2、H2S、烃类等杂质,尤其是烃、苯、COS等对人体有毒有害的杂质都严重超标。这类脱碳解吸气首先要脱硫和高碳烃,然后利用CO2与其他气体杂质沸点的不同实现CO2提纯。
3、高CO2浓度原料气
原料气来源:酒精厂发酵气、油田伴生CO2气源、乙二醇废气、制氢尾气、天然气尾气、炼油尾气、尿素生产中低温甲醇洗工段的尾气等。
主要特点:CO2浓度98%以上,杂质少,含有微量的CH4、N2、CO、H2、H2S、COS、CS2、甲醇、烃类、苯等杂质。在脱硫时需要补充氧气。这类气体提纯液化的工艺流程相对简单,投资低,特别适合生产国际标准的食品级二氧化碳。
针对不同的CO2气源,其液化提纯工艺流程差别较大,原料气中杂质的微量组分对净化工艺也造成较大的差异。因此,在选择/设计CO2液体提纯工艺之前,必须对原料气组分做PPM级别的检测分析。客户也可以委托我们找专业检测机构做样气检测分析。
物理-化学吸收法
化学吸收剂吸收量大,吸收速率较高,分离回收纯度高,但由于发生了化学反应,再生必须通过破坏化学键才能解吸出CO2,因此能耗高,同时化学吸收剂抗氧化能力差,易降解,腐蚀性强,还易出现气泡、夹带现象,因而给工业化应用带来很多困难。物理吸附剂尽管选择性较差,回收率低,但其解吸时不需要破坏化学键,因而能耗比化学吸收剂低。一个很自然的想法是采用物理化学复合吸收剂来吸收CO2,从而兼具物理吸附和化学吸收的有点。
CO2撬装冷箱出厂

CO2回收的主要工艺介绍
针对不同的CO2气源和原料气中杂质微量组分的不同,工艺流程差异较大,但都包含了压缩、脱硫、干燥、净化、液化、提纯、贮存、制冷这八个工艺单元。根据CO2浓度的不同,主要有三类技术:溶液吸收、变压吸附和精馏分离。
1、溶液吸收:适用于CO2含量低的气源,CO2纯度可达~98.5%,气态产品。。
在吸收塔中溶剂溶解了烟道气中的CO2,富含CO2的溶液用泵输送到再生塔中。在再生塔中通过对溶液加热使CO2从溶液中脱离,剩余的溶液降温并加压后用于下一批烟道气脱碳。
在国内外采用众多的脱碳方法中,占主导地位的仍是化学吸收法中添加各种不同活化剂的改良热钾碱法,其中以联碳公司的本菲尔法*突出,且不断开发出新的节能工艺。一乙醇胺法(MEA)由于开发了胺保护法,使这种古老工艺焕发了新的活力。活化MDEA法是德国BASF公司**,国外以天然气为原料的大型氨厂多采用此法。 在物理-化学吸收法中,国内外使用较多的是Norton公司聚乙醇二甲醚法(NHD)和低温甲醇洗法。低温甲醇洗主要用于重油和煤部分氧化法制得的原料气脱硫和脱CO2,与液氮洗脱出微量CO、CH4相匹配,总能耗很低,是一种理想的方法。
2、变压吸附:适用于从合成氨变换气中回收CO2,CO2纯度可达~98.5%,气态产品。 合成氨变换气中主要含有H2、N2、CH4、CO、CO2等组分,此外还含有一定量的杂质组分,如H2O、硫化物等。这些气体组分在吸附剂(如活性炭、分子筛、硅胶)上的吸附能力依次为H20、硫化物>CO2>CH4>CO>N2>H2。变换气先脱水脱硫,然后进入多塔组成的PSA工序,吸附塔依次经过吸附、多次均压降、顺向放压、逆向降压、抽空、多次均压升和*终升压等7个步骤,在吸附塔底边由真空泵抽出解吸的CO2作为产品CO2输出,可生产纯度≥98.5%的CO2。
3、精馏分离:使用于高浓度CO2原料气,CO2纯度可达99.99%,液体产品。
此类原料气的纯度在98%以上,杂质少,将要去除的微量杂质分3类,第一类是硫化物,主要有H2S、COS、CS2,第二类是沸点接近CO2但比CO2略高的物质,例如甲醇、苯、乙烷、丙烷等碳氢化合物,第三类是沸点比CO2低很多的物质,主要有H2、N2、CH2、CO、Ar。
精脱硫技术:通常采用低温有机硫水解催化剂将微量的COS转换成H2S,然后用活性炭精脱硫剂脱除CS2和H2S,脱硫精度为出口H2S≤0.03ppm。
COS+H2O→H2S+CO2 2H2S+O2→2H2O+2S
脱硫的过程需要氧气,如果原料气中没有氧组分,需要补充微量的氧气。
催化氧化技术:催化氧化在精脱硫的基础上,增加催化氧化脱氢、脱烃的净化工序。在特种催化剂下,将原料气中的所有可燃性杂质与氧发生反应,燃烧后产物是CO2和H2O,过程中没有有毒有害物质产生。
2H2+O2→2H2O CnH2n+2+(3n+1)/2O2→nCO2+(n+1)H2O
由于燃烧反应能够**进行,为**去除碳氢化合物和含氧有机物提供了保障。如果可燃组分含量低,催化氧化技术使得能耗增加。目前也采用精馏分离去除可燃组分。
精馏提纯技术:通常采用双塔获得高纯度CO2液体。在T1塔中,甲醇、苯等组分溶解在塔底的CO2液体中,作为残液排出,塔顶排出的原料气经一级冷凝器后部分液化,液体从塔上部进入参与精馏,气体进入二级冷凝器继续降温。从二级冷凝器出来的液体进入T2塔中提纯,气体作为废气排放。在T2塔底边获得CO2纯度≥99.99%的液体CO2产品,T2塔顶部CO2浓度约76%的气体同样作为精馏尾气排放。
通过双塔提纯,将沸点比CO2高的组分从T1塔底边去除,将沸点比CO2低的组分从T2塔顶部排出,从而获得了高纯度的CO2。 我们采用不锈钢填料塔和整体撬装冷箱,制冷剂采用氨制冷或环保制冷剂,从2016年制造了第一套CO2回收装置至今,已制造了20多套CO2回收装置,规模从3万吨/年到30万吨/年,提供生产工业级/食品级CO2液体的成套技术。